Understanding Flat Wire Dimensions
The world of customization extends into the realm of zipper designs innovatively through the use of flat wire dimensions. When we delve into specifics like the 2.4*0.4 and 3.5*0.5 measurements, it's essential to understand what these numbers signify. Essentially, they denote the width and thickness of the flat wire used in crafting zipper teeth or other components. The 2.4*0.4 dimension represents a relatively narrower and thinner profile compared to the 3.5*0.5. Each set offers diverse functionality that caters to different design needs.
Benefits of Using Custom Flat Wire in Zipper Designs
Opting for custom flat wires can significantly elevate the durability of your product by offering enhanced resilience against wear and tear. Beyond strength, custom flat wires improve aesthetic allure, giving zippers a tailored and unique look. These specialized wires allow you to engineer specific functionalities; for instance, smoother operation for lightweight garments or added robustness for heavy-duty applications.
Designing with 2.4*0.4 Flat Wire
The 2.4*0.4 flat wire is ideal for lightweight apparel such as summer dresses or delicate accessories like clutches. Its minimalistic profile makes it perfect for usage where finesse is required without compromising on performance. From an aesthetic standpoint, this slender gauge supports clean, sleek designs. Adding a variety of colors and finishes like matte or glossy enhances its visual appeal further.
Utilizing 3.5*0.5 Flat Wire in Zipper Manufacturing
When it comes to sturdy applications, the 3.5*0.5 flat wire steps up impressively. This size works best for heavy-duty garments like denim jackets or even outdoor gear requiring high endurance under strenuous conditions. Besides imparting a robust look, this larger dimension provides superior strength, making your zippers more resilient.
Steps to Customize Zipper Designs
Your journey towards creating customized zipper designs begins with choosing the right flat wire dimension suited to your product's requirements. Collaborating closely with manufacturers ensures that your vision translates seamlessly into reality. Rigorous prototyping and testing phases are indispensable to guarantee every unit meets the desired quality standards. Constant feedback loops and iterative improvements refine the final output.
Case Studies
Consider the example of a fashion brand leveraging the 2.4*0.4 flat wire to achieve a chic, contemporary aesthetic in their new clothing line. On the flip side, an outdoor equipment manufacturer might employ the 3.5*0.5 flat wire to enhance the durability and functionality of their camping gear products.
Emerging trends indicate a shift towards sustainable materials in zipper manufacturing. Eco-friendly flat wire options such as recycled metals increasingly resonate with environmentally-conscious consumers. Moreover, technological advancements continue to push the boundaries, allowing for innovative design solutions that cater to evolving market demands.
For designers, balancing aesthetics and functionality remains paramount. While striving for visually striking zippers, cost considerations shouldn't be ignored. It's crucial to source high-quality flat wire from reputable suppliers known for consistent delivery standards.
Manufacturing limitations can present hurdles, but addressing these early through thorough planning mitigates risks. Ensuring consistency across large production runs involves strict quality control measures, and overcoming design constraints requires creative problem-solving.
In summary, understanding and utilizing specific flat wire dimensions such as 2.4*0.4 and 3.5*0.5 redefines the possibilities in zipper customization. These elements unlock avenues for innovation, enabling designers to craft unique, functional, and aesthetically pleasing zippers that stand out in a crowded market.
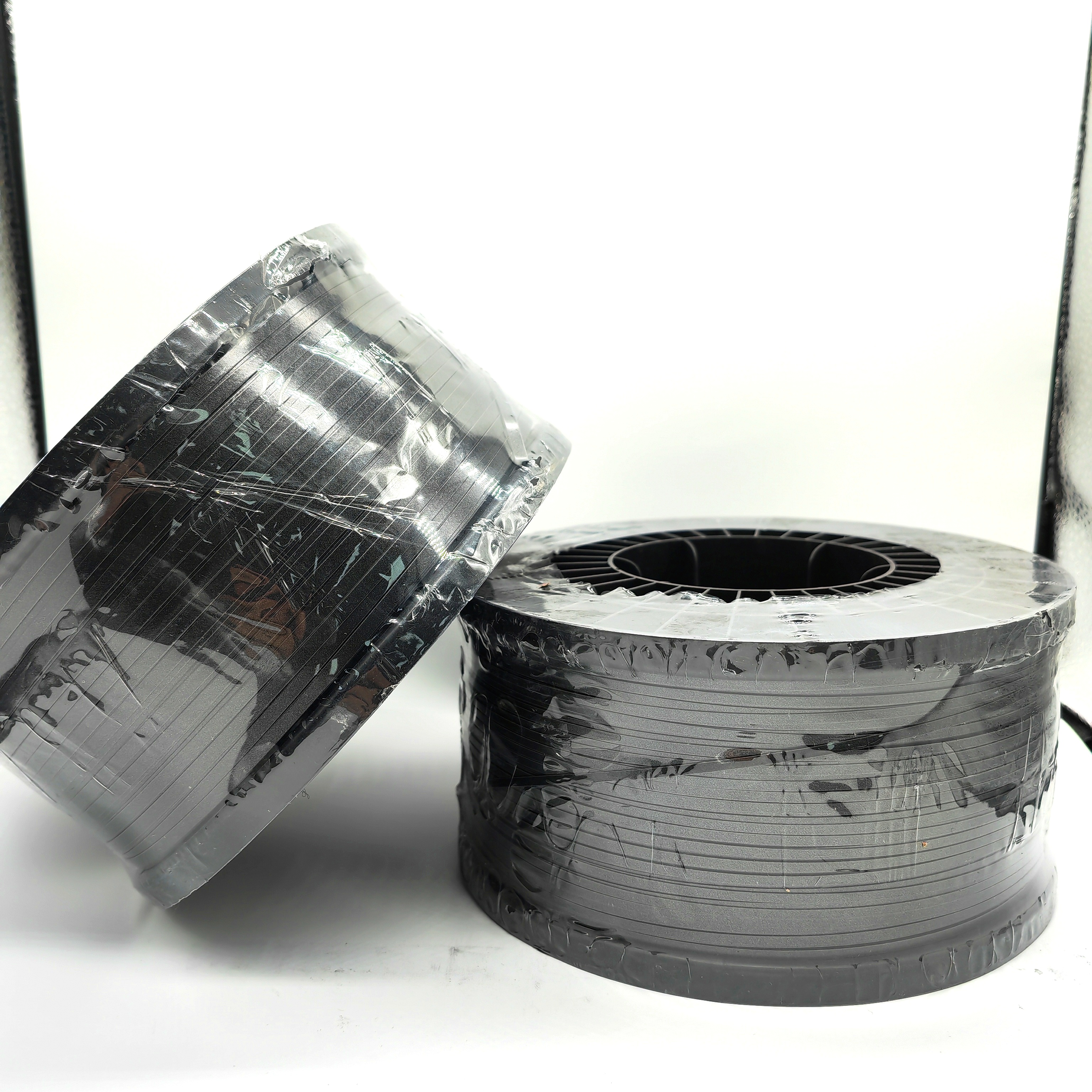